气柜使用中存在的问题
2015/9/6 11:42:42 点击: 文章来源:www.jshhcc.com
工艺状况很差,部分重点工艺指标长期不达标
在公司控 94 项工艺指标中,有 19 项指标长期不达标。比如,气柜核心工艺指标炉顶空间温度,设计值为 800±50℃。但公司气柜自投产以来一直高达 930-960℃,最高达到 1000℃。炉顶空间温度偏高,直接导致焦油、粗苯等化产品产率低、焦油质量差,生产系统不稳定。
温度制度及执行情况不好
燃烧室所有立火道任一点的温度不得超过 1450℃,不得低于 1100℃。有部分立火道温度低于 1100℃。长结焦时间标准温度不得低于 1100℃,炉头温度不得低于 950℃。炉头温度在 700℃左右。炉头温度与标准测温火道温度之差应小于 150℃。生产中大于 150℃。炉顶空间温度 800±50℃。生产中一般在 930-960℃,最高达到 1000℃。直行温度平均值与标准温度相
差在±7℃以内,生产中相差较大。
气柜核心工艺指标炉顶空间温度,设计值为 800±50℃。但公司气柜自投产以来一直高达 930-960℃,最高达到 1000℃。炉顶空间温度偏高,造成部分煤气裂解,直接导致焦油、粗苯等化产品产率低、质量差。炉顶空间温度过高,导致焦油粘度大,初冷器阻力大,焦油氨水系统运行不正常,煤气净化效果差,导致回炉煤气中焦油、萘等杂质含量较高。造成加热煤气系统设备堵塞严重,回炉煤气流量波动较大,炉温波动大、加热不均匀。
工艺指标要求炉头温度不得低于 950℃,但生产中炉头温度基本上低于控制指标,一般在 700℃左右。炉头温度过低,一方面炉头部位的焦炭不能按时成熟,易造成推焦困难;另一方面会造成装煤后炭化室炉头部位墙面温度降到硅砖晶形转化点以下,造成炉头砖损坏严重,气柜的密封性降低,气柜煤气中氮气含量增加。我公司配套建有 20 万吨气柜煤气造甲醇项目,要求气柜煤气的氮气含量指标,设计值为 4%。但公司气柜自投产以来一直持续攀升,从未达到设计值。其中,2006 年平均值为 10.3%,2007 年平均值为 12.3%,2008 年平均值为 18.6%,2009 年平均值为 19.5%,2010 年 1-9月份,平均值为 28.03%,最高达到 34%。氮气含量超标,降低了甲醇合成效率,直接影响了甲醇产量。
压力制度及执行情况不好
燃烧室立火道看火孔压力应保持 0~5Pa。生产中一般负压。单个蓄热室顶部吸力与同侧蓄热室顶部平均吸力相比,上升气流为±2Pa,下降气流为±3Pa(边炉除外)。集气管压力 160Pa(7.63 米气柜)。生产中一般控制在 40pa 以下。
集气管压力要求保持在 160pa。由于开工初期,化产风机频繁跳车及偏流,同时放散点火长久未能实现自动,导致事故状态下炉门等设备不能及时得到保护,并且国际焦化煤气用户单一,每次气柜加热系统换向,都给集气管压力带来较大的压力波动,导致气柜加热换向期间炉门冒烟冒火,炉门、炉体密封每况愈下,集气管压力被迫降低,一般控制在 40pa 以下。
炭化室负压操作,空气进入炭化室,加剧了炉门炉框的烧损,形成了恶性循环,气柜状况逐渐恶化。
炭化室负压操作,空气进入炭化室,加剧了炉门炉框的烧损,形成了恶性循环,气柜状况逐渐恶化。
利旧设备故障频发,维持生产异常困难
据统计,2007 年至 2009 年,因四大车(推焦车、拦焦车、熄焦车、装煤车)、叶轮放焦机、煤气鼓风机等二手设备原因引发的计划外检修高达 26次,其中,2007 年 7 次,2008 年 9 次,2009 年 10 次;引发的计划外停车高达 49 次,其中,2006 年 15 次,2007 年 18 次,2009 年 16 次。频繁检修停车,直接导致系统不能长周期稳定运行,给安全生产构成重大隐患。特别是 2010 年,气柜设施严重受损,炭化室炉头部位严重剥蚀、穿孔,个别炭化室炉墙变形,炉门框断裂、错台,荒煤气导出设备及小炉门严重损坏。炉门、炉框、上升管更换频繁,维修量加大,生产成本急剧增加。炉门难摘难挂、人工扒焦等异常现象呈上升趋势,“推焦难”已十分突出,维持生产异常困难。
产品产量低,长期不能达产达效
投产以来,产品产量与设计差距较大。产品产量低,直接导致成本高、消耗大,无法形成正现金流,经营严重亏损。各产品产量情况见表 2-2。
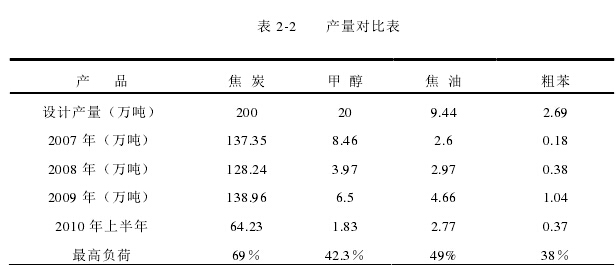
经营效果差,亏损严重
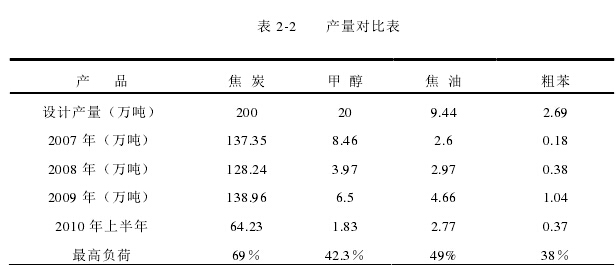
从 2006年至 2010年上半年,公司累计亏损 9.96亿元,为资本金的 113%,其中,2006 年亏损 3670 万元,2007 年亏损 8108 万元,2008 年亏损 3.50亿元,2009 年亏损 3.82 亿元,2010 年上半年亏损 1.46 亿元。折旧、财务、薪酬“三项费用”,2006 年为 2831 万元,2007 年为 2.48 亿元,2008 年为2.75 亿元,2009 年为 3.38 亿元,2010 年上半年为 1.17 亿元,除 2007 年外其它年份现金流均为负值。目前,公司资金链时刻面临断裂危险,已成为银行的重点关注单位。
生产运行极不稳定,安全环保压力巨大
重点工艺指标严重超标,给系统运行带来了一系列隐患,且长期得不到有效治理,严重影响了安全生产和达标排放。特别是 2010 年以来,气柜及护炉铁件严重受损,生产环境和工艺状况进一步恶化,烟气时常超标排放,公司已成为地方环保部门的重点监控对象,装置系统的不可靠,已构成重大安全隐患。
造成问题的原因
兖矿国际焦化从德国引进的亚洲最大 7.63 米气柜在引进、消化吸收方面存在较大差距。项目初衷就是原拆原建,设计院在没有完全理解消化吸收德国技术的条件下,只能照抄照搬,保持原拆原建原则,设计水平还停留在德国的 80 年代技术水平上,在气柜本体上、控制手段上、配套的煤气净化上已经落后于现在的新上的同等规模的大型气柜的技术水平;国内煤炭资源分布和储量与德国存在较大差异,入炉煤配比和指标控制存在客观差异,炉子引进后存在水土不服问题。
气柜加热水平小
气柜设计加热水平为 1210mm,后来的太钢、马钢、武钢都维持现有的设计数据,但通过运行都存在炉顶空间温度高的问题。首钢曹妃甸项目气柜加热水平调整至 1440mm,沙钢增加到 1500mm,经对比,沙钢燃烧室的降低不仅满足了炉顶空间温度的降低的要求,同时保证了焦炭上下能够均匀成熟,运行效果较好。
根据炼焦工艺设计,炼焦所需热量必须全部由燃烧室经炉墙传导给炭化室内的配合煤。加热水平是指炭化室与燃烧室的高度差,炭化室宽度为炭化室横向距离。由于炼焦过程配合煤体积逐步缩小,必须根据配合煤挥发性选择合理的加热水平和炭化室宽度,才能保证燃烧室热量始终经炉墙传导给配合煤。但基于国内配合煤收缩大现实,公司气柜的 1210mm 加热水
平相对较低,使得气柜在结焦末期燃烧室部分区域经炉墙直接加热炭化室,导致炉顶空间温度偏高。而公司 623mm 炭化室为世界上最宽的炭化室,炭化室过宽使得焦饼在炭化室内横向、纵向收缩较大,进一步加大了结焦末期燃烧室经炉墙直接加热炭化室的面积,促使炉顶空间温度进一步升高。炉顶空间温度偏高,一是导致气柜煤气有效成份发生裂解,造成化产品回收率低,焦油质量不合格,严重影响效益;二是导致焦油粘稠,化产部分设备堵塞严重,化产系统运行效率下降。而化产系统运行效率下降,进一步降低了化产品回收率,降低了回炉煤气质量,增加了气柜调火困难,影响了气柜正常加热,使炉顶空间温度更难控制;降低了甲醇原料气净化度,净煤气中焦油、萘等杂质超标,导致甲醇生产不稳定。为此,低加热水平和宽炭化室,是公司生产不稳定的根源所在。
平相对较低,使得气柜在结焦末期燃烧室部分区域经炉墙直接加热炭化室,导致炉顶空间温度偏高。而公司 623mm 炭化室为世界上最宽的炭化室,炭化室过宽使得焦饼在炭化室内横向、纵向收缩较大,进一步加大了结焦末期燃烧室经炉墙直接加热炭化室的面积,促使炉顶空间温度进一步升高。炉顶空间温度偏高,一是导致气柜煤气有效成份发生裂解,造成化产品回收率低,焦油质量不合格,严重影响效益;二是导致焦油粘稠,化产部分设备堵塞严重,化产系统运行效率下降。而化产系统运行效率下降,进一步降低了化产品回收率,降低了回炉煤气质量,增加了气柜调火困难,影响了气柜正常加热,使炉顶空间温度更难控制;降低了甲醇原料气净化度,净煤气中焦油、萘等杂质超标,导致甲醇生产不稳定。为此,低加热水平和宽炭化室,是公司生产不稳定的根源所在。
装煤时煤气导出吸力不足
德国原设计装煤车带有跨越管,在装煤车装煤时,煤气导出采用装煤车上煤气导出系统配合高压氨水装煤进行操作。装煤车上的跨越管使正在装煤的炭化室的装煤孔与相邻的处于结焦末期的炭化室装煤孔导通,将部分荒煤气抽吸到相邻炭化室中,配合高压氨水喷射实现无烟装煤。鞍山焦耐院再设计时取消了装煤车煤气导出系统,仅保留了高压氨水装煤,造成装煤时煤气导出动力不足,仅能实现 80%的烟气的吸入,冒烟冒火严重,多次出现烧装煤车事故,污染环境。相比沙钢及国内其它后来 5 家 7.63 米气柜均为 PROVEN 系统,集气管负压操作,保证装煤过程不冒烟冒火,同时又能确保结焦末期炭化室底部微正压,恰到好处的解决了装煤冒烟冒火和炭化室负压操作的矛盾。
气柜机械功能差距大
兖矿国际焦化公司的气柜机械是由国内大连重工公司对德国夏尔克产品的国内恢复,大部分功能没有恢复,现在只是实现了基本的生产功能,造成车辆效率低,与其它几个国内后来建设的 7.63 米气柜四大车功能相比差距太大,他们都实现了一键操作:自动对位、自动减速、自动推焦、拦焦、熄焦等等。安全可靠,杜绝了事故的发生,提高了生产效率。国际焦化公司气柜机械没有实现一点定位系统下的一键操作,清门清框等不能运行,生产全靠对讲机联系,车辆也不能自动减速,效率低,易误操作。大小炉门更换及修理的速度跟不上,清门清框功能未恢复等原因造成炉门密封不严,漏空气严重,造成炉顶空间温度高,上升管烧坏,安全生产极没有保障。
该焦化设备在德国凯厂已运行 8 年,未加保护停产 4 年,解体拆迁到安装开车又是 4 年,总计 16 年。设备损坏、锈蚀比较严重,更新配套难度大,其“先进性”已不可同日而语。气柜机械和气柜设备均为利旧设备,可靠性降低,故障率较高。四大车功能低,有些重要功能大连重工集团一直未能完全恢复,仅具备基本功能,至今清门清框、四车通讯和一点定位等重要自动功能仍未完全恢复,降低了推焦效率,也影响了安全生产和气柜工艺操作。炉门、炉柱等护炉铁件,虽然经过修配改,但其密封性能已有下降,且随着生产周期延长,护炉铁件变形严重,炉体密封状况越来越差。
宽炭化室对生产影响大
宽炭化室大容积气柜的焦饼在炭化室内横向和纵向收缩较大, 焦饼与炉墙间隙大。因此,如果使用高挥发分配煤炼焦时,会使炉墙和炉顶空间生成大量石墨。因而弱粘结性的气煤配入量必须予以限制,在德国仅限 15%。国内配合煤指标与德国配合煤指标差距大,原设计在德国入炉煤挥发份指标控制在 22-24%,配煤以主焦煤、肥煤、瘦煤为主。由于国内煤资源分配非常不平衡,且以低变质程度的高挥发分煤源为主,肥煤、主焦煤、瘦煤为稀缺煤种,实际配合煤挥发份达到 29%,受炼焦原料煤挥发分高、收缩率大影响,造成煤气产量大,炉顶空间大,气柜气停留时间长,炉顶区及上升管处结石墨严重。由于挥发分高和气柜进空气使得煤气气量在焦炭生产只有 80%的负荷下,煤气量超过了设计值,最高时已经达到了 13 万立方米每小时,一般在 11~12 万立方米每小时,造成整个化产工序负荷高,鼓风机满负荷运行。同时造成的另一个问题就是焦油质量差、粘度大,流动性差,产品质量不合格。经常堵塞设备和管道,化产超级离心机无法实现连续运转,焦油不能输送到罐槽中,只能就地装车。与我们气柜相同的沙钢配合煤指标中挥发份一般控制在 26%左右,马钢也逐渐将挥发份控制在 27%左右,沙钢的炉顶空间温度在 860℃左右,由于他们的炉顶空间温度控制较好,其上升管内部非常光洁,无结石墨等现象发生。
荒煤气中氮气含量高
荒煤气中氮气含量高
7.63 米气柜由于存在炭化室高、密封面积大,容易造成空气的吸入,普遍存在氮气含量高,都没有达到国内 6 米以下炉子 4%含量的指标,一般在 5%以上,马钢、太钢、武钢在 8-10%,沙钢、首钢在 6%左右,而国际焦化公司气柜氮气含量,一般在 15%以上,荒煤气品质差。
集气管压力控制手段少
国际焦化公司每座气柜采用三段集气管,这三段集气管又相互连通,因此三段之间存在严重的相互干扰,三段集气管的控制也不平衡。在气柜加煤操作时,由于瞬时产生大量荒煤气,该炭化室上升管压力迅速上升,使本段集气管压力随之上升,并影响到其它两段集气管压力。造成集气管压力失衡,变得不稳定;再有交换机在交换时,因加热煤气管道上没有大
容积缓冲气柜,不能很好的消除气柜换向过程时带来的干扰,造成集气管压力增大 40 多帕,使各小炉门出现冒烟冒火现象;荒煤气中部分杂质粘凝在初冷器和煤气管道内,导致阻力变化,风机的实际吸气量改变,进而影响集气管压力。目前气柜监控系统、冷鼓监控系统已经投入运行。但集气管压力基础调节设计放在气柜监控系统内,然而与集气管相关的初冷器前
吸力和风机转速调节等功能设计仍在冷鼓监控系统,集气管压力调节实际上分散在炼焦车间和化产车间,没有实时的协调和联动,加上煤气鼓风机设备本身风量偏小,风压低没有调节余地,至今无法实现集气管压力自动控制。
容积缓冲气柜,不能很好的消除气柜换向过程时带来的干扰,造成集气管压力增大 40 多帕,使各小炉门出现冒烟冒火现象;荒煤气中部分杂质粘凝在初冷器和煤气管道内,导致阻力变化,风机的实际吸气量改变,进而影响集气管压力。目前气柜监控系统、冷鼓监控系统已经投入运行。但集气管压力基础调节设计放在气柜监控系统内,然而与集气管相关的初冷器前
吸力和风机转速调节等功能设计仍在冷鼓监控系统,集气管压力调节实际上分散在炼焦车间和化产车间,没有实时的协调和联动,加上煤气鼓风机设备本身风量偏小,风压低没有调节余地,至今无法实现集气管压力自动控制。
护炉铁件损坏严重
受气柜顶空间温度高、初冷器阻力大、经常造成煤气鼓风机偏流(不打量),气柜煤气导出受阻,特别气柜刚生产时,甲醇缓冲气柜和焦炉自动放散不能投用,造成气柜冒火,对气柜损害较大。
受初冷器的影响,风机频繁的偏流,造成了护炉铁件损坏,对炉体保护能力下降。机焦侧炉门框断裂、错台;部分炉柱变形扭曲,机焦侧炉门损坏,密封效果差,炉门难摘难挂现象较多,已影响正常生产操作;弹簧烧损失效,弹簧顶丝变形,部分小炉门损坏,装煤时无法进行平煤操作。其次炭化室长期负压操作,气柜损坏。大多数炭化室炉头部位炉墙剥蚀,个别炉号出现明显的炉墙纵缝,局部炉墙的炉头穿孔倒塌。部分炭化室炉墙变形严重,焦侧炭化室变窄,影响生产和安全推焦操作,以及荒煤气导出设备损坏,上升管根部烧穿,集气管变形,部分发生扭曲,个别桥管翻板无法正常启闭。
受初冷器的影响,风机频繁的偏流,造成了护炉铁件损坏,对炉体保护能力下降。机焦侧炉门框断裂、错台;部分炉柱变形扭曲,机焦侧炉门损坏,密封效果差,炉门难摘难挂现象较多,已影响正常生产操作;弹簧烧损失效,弹簧顶丝变形,部分小炉门损坏,装煤时无法进行平煤操作。其次炭化室长期负压操作,气柜损坏。大多数炭化室炉头部位炉墙剥蚀,个别炉号出现明显的炉墙纵缝,局部炉墙的炉头穿孔倒塌。部分炭化室炉墙变形严重,焦侧炭化室变窄,影响生产和安全推焦操作,以及荒煤气导出设备损坏,上升管根部烧穿,集气管变形,部分发生扭曲,个别桥管翻板无法正常启闭。
加热交换系统存在问题
气柜加热用的煤气、空气和燃烧后的废气在加热系统内的流向由液压交换机驱动交换传动装置来控制,每隔 20-30min 换向一次。气柜地下室加热用煤气换向时,由于没有煤气缓冲装置,化产鼓风机
压力自调装置没有投用,也引起气柜集气管压力的较大波动。气柜集气管压力的较大波动,都会出现气柜门冒烟冒火现象,烧坏炉门、炉门框、弹簧等护炉铁件,炉门密封不严、损坏炉体并造成氮气含量的增加,影响甲醇产量。
压力自调装置没有投用,也引起气柜集气管压力的较大波动。气柜集气管压力的较大波动,都会出现气柜门冒烟冒火现象,烧坏炉门、炉门框、弹簧等护炉铁件,炉门密封不严、损坏炉体并造成氮气含量的增加,影响甲醇产量。
环境存在污染
在实际生产过程中,对环境造成污染主要表现在两个方面:一是装煤时烟尘严重超标,大量荒煤气从炉顶装煤孔处露出,高压氨水系统不能有效消除装煤烟尘;二是初冷器堵塞或系统波动时气柜放散对环境造成污染。
这些问题的存在和长期无法解决给国际焦化公司带来了巨大的压力,安全、环保、效益等方面存在较大难题。公司决定于 2011 年开始对气柜及配套系统实施改造。
这些问题的存在和长期无法解决给国际焦化公司带来了巨大的压力,安全、环保、效益等方面存在较大难题。公司决定于 2011 年开始对气柜及配套系统实施改造。